Electromagnetic control of liquid metal layer dynamics
Contactless methods are essential in many modern technological processes to move and control liquid metals. For example, a novel energy-efficient alternative to the “classical” multi-stage continuous casting process, where initial square-cut ingots are repeatedly heated and rolled in a roller system to obtain thin steel strips, is the direct strip casting, where liquid metals are poured onto an intensively-cooled moving belt. In this process, liquid metal flow and motion of the free surface must be controlled to ensure a stable process and high quality of the final product.
As high-temperature alloys (above 1000°C) are very aggressive, mechanical liquid metal flow management techniques are disadvantageous. Efficient solutions can be provided by contactless electromagnetic (EM) technologies, which allow moving and controlling liquid metals using magnetic field. In order to explore different aspects of the interaction between high-frequency EM field and a thin liquid metal layer, researchers from the Institute of Numerical Modelling, in cooperation with colleagues at the Institute of Electrotechnology (ETP), Leibniz University Hannover, conducted a series of experiments where stability of a thin liquid Galinstan layer was studied under different EM field configurations.
By changing relevant system parameters, such as the electric current, melt layer thickness and initial shape, development of instabilities and different free surface shape transformations were observed. The experimental results will be further analysed and interpreted, and will be used to validate complex numerical models that describe the underlying physical processes. Experimentally validated and tested numerical models can further be used to design and optimize different technological processes.
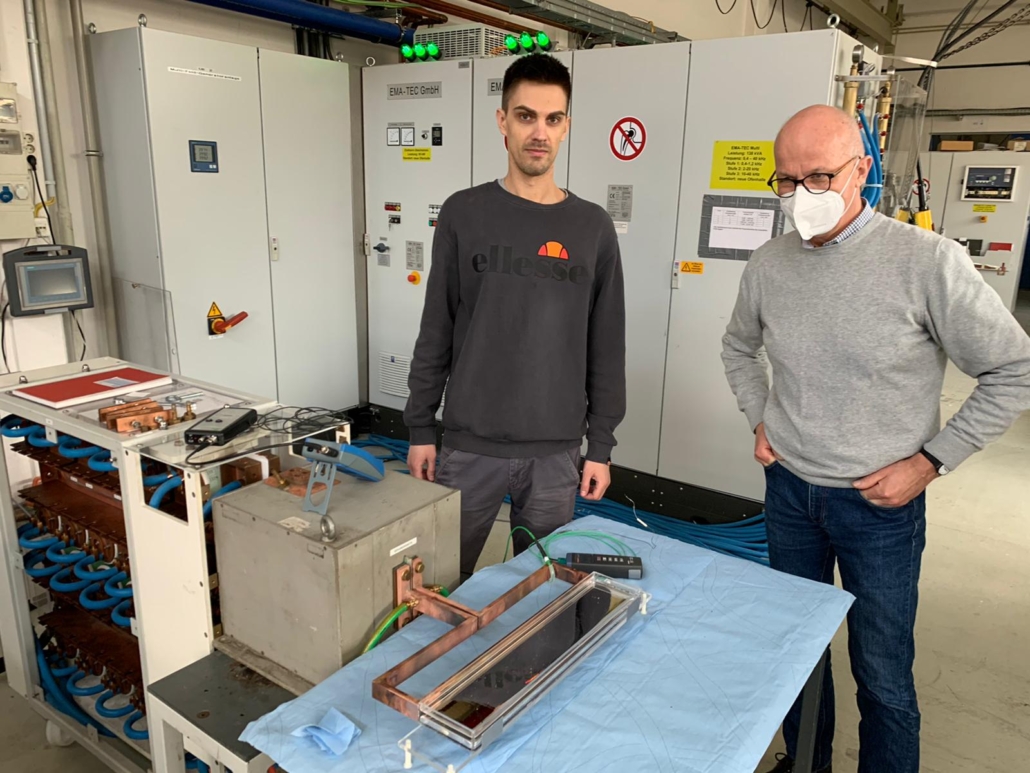
The studies are carried out in the framework of the ERDF project “Development of numerical modelling approaches to study complex multiphysical interactions in electromagnetic liquid metal technologies” (No 1.1.1.1/18/A/108).